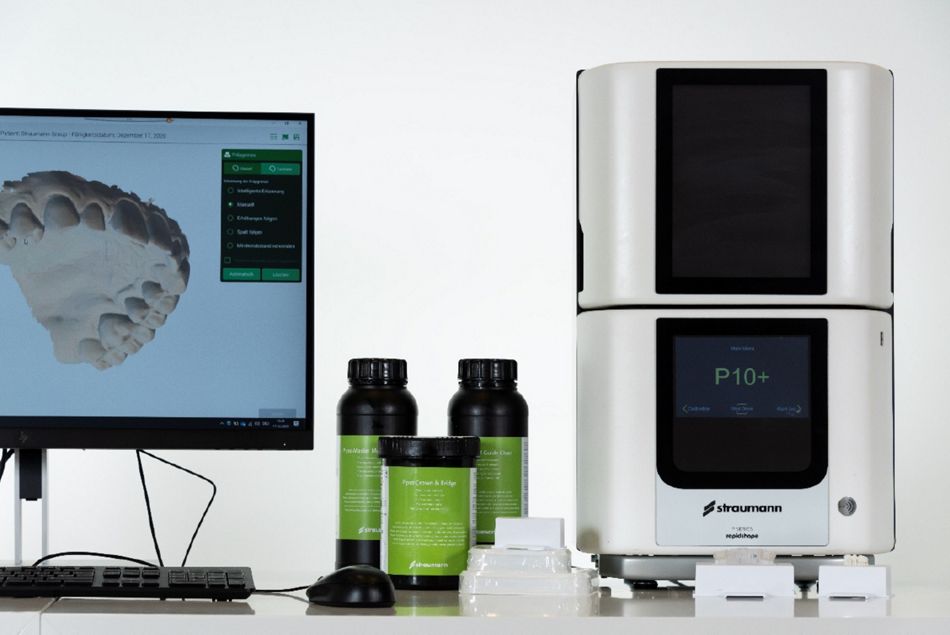
3D printing, also known as additive manufacturing, has been an ally among dental practices worldwide. Over the past decade, there have been more and more examples of clinics implementing this technology to create surgical tools, aligners, dentures, and aid implantology, reducing the need for outsourcing. This disruption has also proven to be a method of education for dental practitioners and patients through in-house digitized processes. Recognising the benefits of 3D printing in dentistry, Professor Lior Shapira, President of the European Federation of Periodontology (EFP), stated: “The digital approach is more accurate, shortens the surgical procedure, and has fewer adverse effects.”
Streamlining customised production
No one set of teeth is alike. Considering this, dental prostheses must be produced with customisation as a priority. Conventionally, this is done through CAD/CAM milling technology. As a form of subtractive manufacturing, milling can result in material wastage and calls for further manual crafting from technicians. Moreover, prostheses made through traditional methods have limitations when complex anatomy is involved. There are also restrictions regarding the volume at which crowns, implants, dentures, and other dental devices can be manufactured.
With 3D printing technologies, printed crowns and alike can be produced in various volumes in-house to avoid outside interference.
Even though dental prostheses are explicitly designed for one patient, having multiple at a dentist’s disposal would be an asset. There have been cases where the integrity of a crown has been compromised due to storage conditions and temperature changes during their transportation from a clinic to a laboratory. This leads to the crown being unfit for its intended patient. As a result, the overall restoration process will be prolonged as dental professionals have to spend time creating a new model or doing all they can to salvage the initial prosthetic. With 3D printing technologies such as Selective Laser Sintering (SLS), Stereolithography (SLA), and Digital Light Processing (DLP), 3D printed crowns and alike can be produced in various volumes in-house to avoid outside interference. This allows more room for error as technicians won't be starting from scratch when making the necessary adjustments.
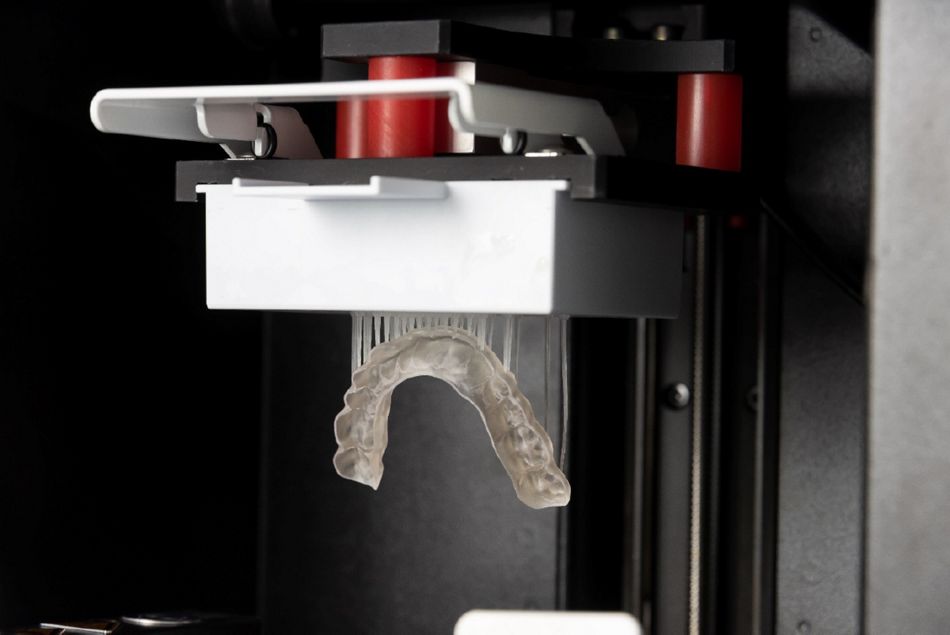
SLS technology uses lasers to fuse nylon-based powders to print objects. This process does not use support structures for additive manufacturing. SLA, on the other hand, uses a moving UV laser to cure resins into objects. Conversely, DLP utilises stationary UV light from a projector to cure full layers of resin. Demonstrating the benefits of 3D printing, earlier this year, a 3D printed temporary crown using the Straumann composite resin P pro Crown & Bridge was created to support the process of immediate implant restoration. During this process, the Straumann® CARES® P20 3D printer, which is built upon DLP technology, was used. This case states that the use of DLP technology enabled accelerated production as opposed to SLA and conventional methods.
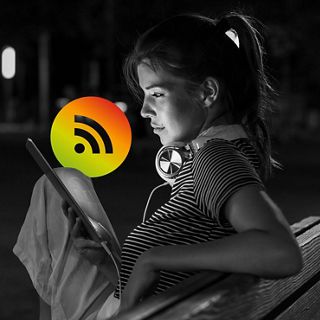
Want to stay up to date?
youTooth.com is THE PLACE TO BE IN DENTISTRY – subscribe now and receive our monthly newsletter on top hot topics from the world of modern dentistry.
Creating a digital patient
In addition to speeding up customisation, additive manufacturing has worked in tandem with data collection processes to optimise treatment plans and patient communication. With AI and algorithmic advancements in 3D imaging, CBCT and MRI data can be efficiently collected, cleaned, and stitched with 3D meshes to create a vivid simulation of a patient’s oral condition. This data, commonly referred to as a “Digital Patient”, can be converted into a printable STL file which is then used to make 3D printed bone-supported, mucosa-supported, and other tooth-supported surgical guides. This data can also be used to create 3D printed anatomical models which both patients and dentists can use as a visual reference before a procedure.
When using 3D printing digital solutions, guides can be made and post-processed in a dental practice
Without the use of additive manufacturing, guides such as diagnostic casts can be made from alginate impressions. Vacuum forming over such casts is also a method used to create radiographic guides. These dental appliances are often milled manually to make holes that aid in positioning an implant. Such processes are restricted in some capacity as special equipment is required which is not found in dental practices. Moreover, the average dental practitioner needs a solid amount of experience to operate the machinery involved. On the other hand, when using 3D printing digital solutions, guides can be made and post-processed in a dental practice.
In-house 3D printing has been shown to reduce a patient’s overall treatment time and improve the precision of implant placement as alterations can be efficiently made. In some cases, during a patient's treatment plan, improved digital documentation enables a dentist and patient a more in-depth view of virtual 3D models before fabrication. In doing so, patient concerns can be quelled as they can visualise what their treatment will entail. More accurate surgical predictions can also be made with new digital workflow software. On top of this, 3D printed scaled anatomical models can be used as study devices for dentists and patients. Patients with unique oral anatomies can physically see their problem areas with these tangible tools. Dentists are then able to use these models for future training on more complicated cases. A study led by Oral Medicine and Radiology, PAHER University states:
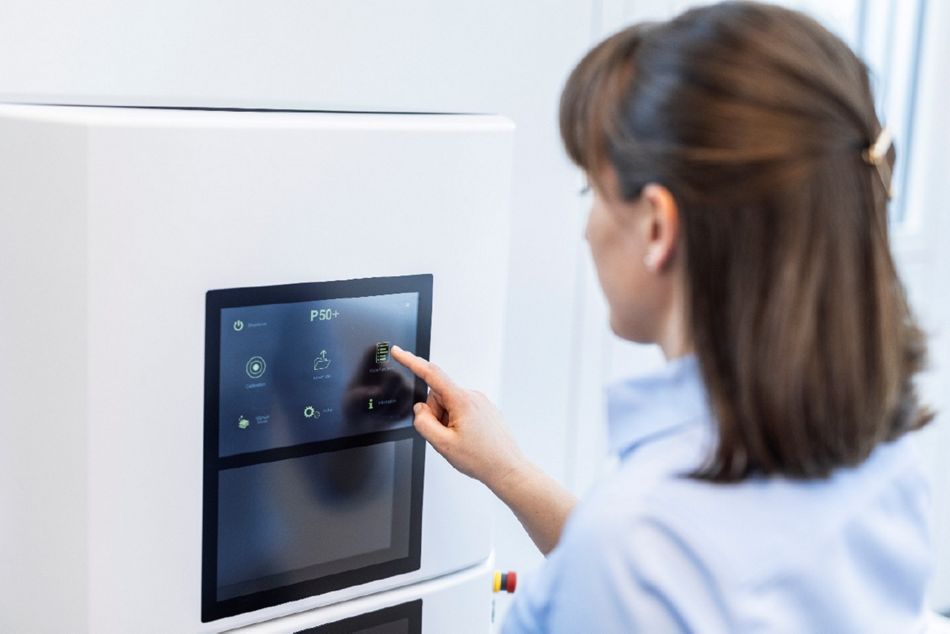
“Models prepared with 3D printing are very useful for teaching students in endodontics, as well as it increases perception of normal or complex canal anatomies, root types and tooth morphology and various canal preparation technical steps such as access cavity preparation, and cleaning-shaping of the root canal can be simulated.”
Overriding overheads
In orthodontics, 3D printing has demonstrated a rather significant impact within dental clinics. As an alternative to traditional braces, clear aligners can be created with the help of 3D printed dentition models and thermoforming. This once again eliminates overhead as all of the production is done within the practice. Furthermore, the patient can reduce the number of times they have to visit their dentist for cleaning, and tightening or loosening wired braces.
Having a high-end 3D printer, in the practices, reduces the annual running costs
In some scenarios, particularly during the height of the COVID-19 pandemic, clear aligner delivery services have been curated which completely cut out the need for a patient to step foot into a clinic. The patient simply takes their own impression using a provided kit and sends it back to the clinic. Their aligners are then promptly produced with the aid of 3D printers and sent to their houses. Following this, they can monitor the positioning progress of their teeth using a smartphone app. Observing such disruptive technologies, the global clear aligners market is projected to grow from USD$2.85 billion in 2021 to USD$10.04 billion in 2028 at a compound annual growth rate (CAGR) of 19.7%, according to Fortune Business Insights. The study states: “Key players' growing competition for advanced product launches for scanning and 3D printing is anticipated to boost the market during the forecast period.”
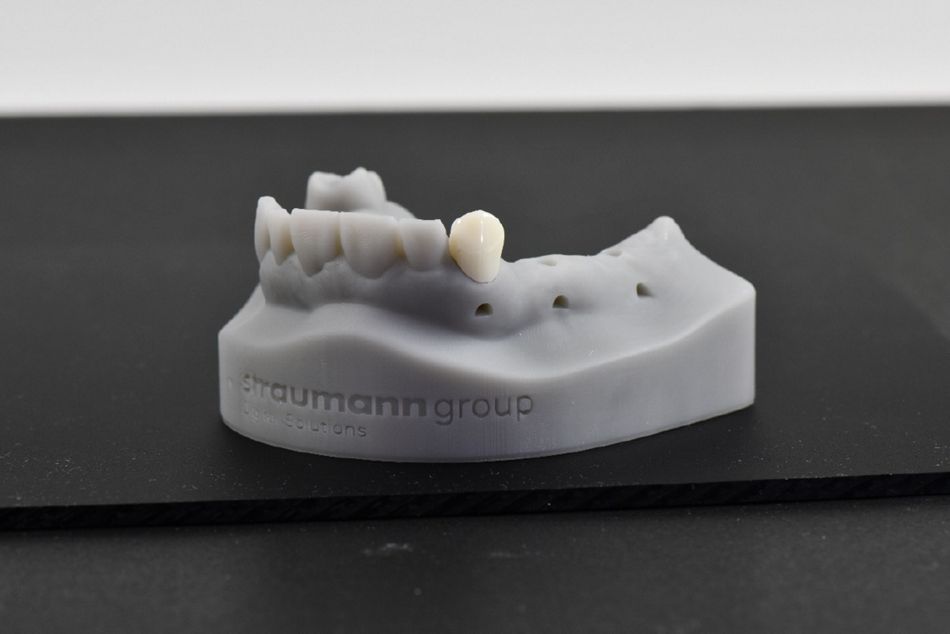
The elimination of overhead has proved financially beneficial for both dental practices and patients. Members of the American Dental Association (ADA) have highlighted that having a high-end 3D printer, with an upfront cost around USD$20,000 in their practices, has reduced their annual running costs which are estimated to be around USD$100,000. Dr. Angela Evanson, DDS, explains that additive manufacturing can lower overhead costs by 80%. These savings can then trickle down to the patient in the form of more affordable dental care. Productivity can also be increased with a 3D printer as practice staff are free to work efficiently on other tasks while a model is being manufactured. This would not be the case when crafting traditional models.
Final thoughts
3D printing continues to change the way dental practices treat their patients. And with no clinic wanting to be left behind, the adoption of new technologies such as this doesn’t seem to be stopping. Nonetheless, competitiveness doesn’t seem to be the driving factor for the move from analogue to digitised dental methods. The numerous cases that have demonstrated the value 3D printing has provided in customisation, treatment planning, surgical procedures, practice productivity, and cost-efficiency, have all been influential in modernising dental care.
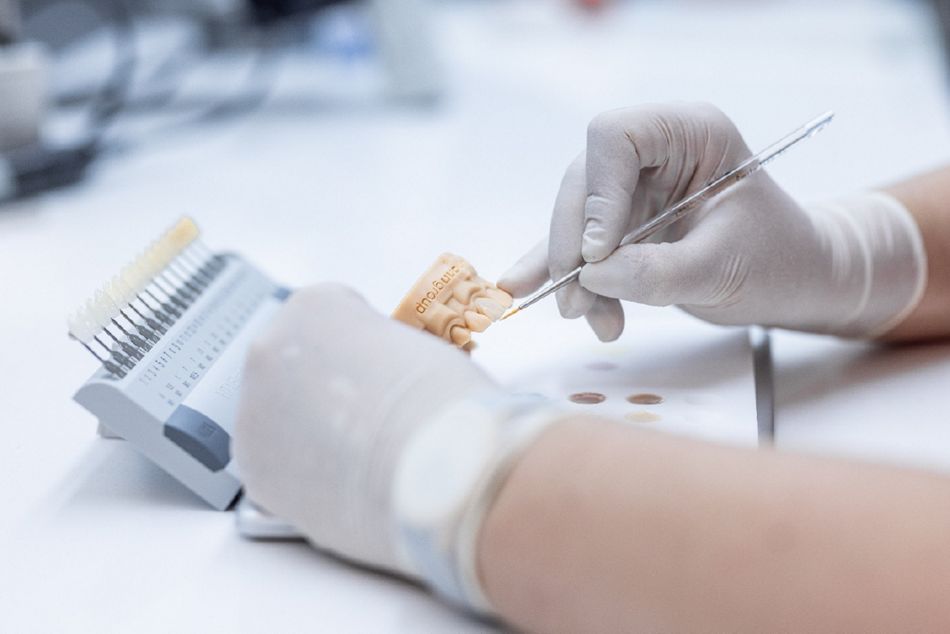
Nevertheless, there are several challenges that need to be faced when using 3D printing technologies. Despite the automation involved in the actual printing of a model, there is a learning curve for the average dental practitioner in understanding how to operate a 3D printer effectively. Once this hurdle is jumped, they can be confident enough to fabricate a selection of models to support their patients, as well as handy tools to help with the day-to-day operations of their clinic. In addition to this, materials compatible for dental applications are still in need of development and validation. Even so, this only amplifies the anticipation and further revolutionization of 3D printing in dentistry.
Further Reading:
Want to learn more about how 3D printing is revolutionising dentistry? Check out these articles:
Sources:
- Clear Aligners Market Size, Share & COVID-19 Impact Analysis, By Patient Age Group (Teenager, and Adults), By End-User (Hospitals, and Dental & Orthodontic Clinics), and Regional Forecast, 2021-2028. [online] Available at: https://www.fortunebusinessinsights.com/industry-reports/clear-aligners-market-101377.
- Evanson, A. (2016). How 3D Printing Is Revolutionising Dentistry. [online] Angela S. Evanson, DDS. Dentist in Parker, CO. Available at: https://www.evansondds.com/how-3d-printing-is-revolutionizing-dentistry/
- Özcan, M. (2021). Grand Challenges in Reconstructive Dentistry [Review of Grand Challenges in Reconstructive Dentistry]. Frontiers in Dental Medicine. https://www.frontiersin.org/articles/10.3389/fdmed.2021.604776/full
- Pigliacelli, S. (2021). The crown the lab made doesn’t fit: Why does this happen? [online] Perio Implant Advisory. Available at: https://www.perioimplantadvisory.com/restorative-dentistry/lab-considerations/article/14209670/the-crown-the-lab-made-doesnt-fit-why-does-this-happen.
- Ramasamy, M., Giri, Raja, R., Subramonian, Karthik and Narendrakumar, R. (2013). Implant surgical guides: From the past to the present. Journal of Pharmacy & Bioallied Sciences, [online] 5(Suppl 1), pp.S98–S102. doi: 10.4103/0975-7406.113306.
- Shaikh, S., Nahar, P., Shaikh, S., Sayed, A. Jamal and Mohammed Ali, H. (2021). Current perspectives of 3d printing in dental applications. Brazilian Dental Science, [online] 24(3). doi: 10.14295/bds.2021.v24i3.2481.